Technologies rapides et précises avec une longue durée de vie
Le thermoformage, également appelé durcissement par compression, est utilisé pour fabriquer des pièces de carrosserie particulièrement résistantes. En début de ligne, les platines sont séparées de manière classique, puis transportées à travers un four où elles atteignent des températures supérieures à 900 °C. Elles sont ensuite formées à haute température. Il est alors important d’avoir des temps de chargement rapides afin d’éviter un refroidissement trop important. Cette application est donc idéale pour les systèmes d’alimenteurs transversaux. Au cours de la dernière décennie, SIEMPELKAMP Transport Systems a automatisé avec succès de nombreuses installations de thermoformage à différents niveaux d’extension standardisés. Pour cela, deux solutions différentes sont en principe utilisées en fonction des exigences : le concept d’alimenteur et le concept de transfert.
Vue d’ensemble du système
Début de ligne
Chargement et déchargement de la presse
Début de ligne : Structure
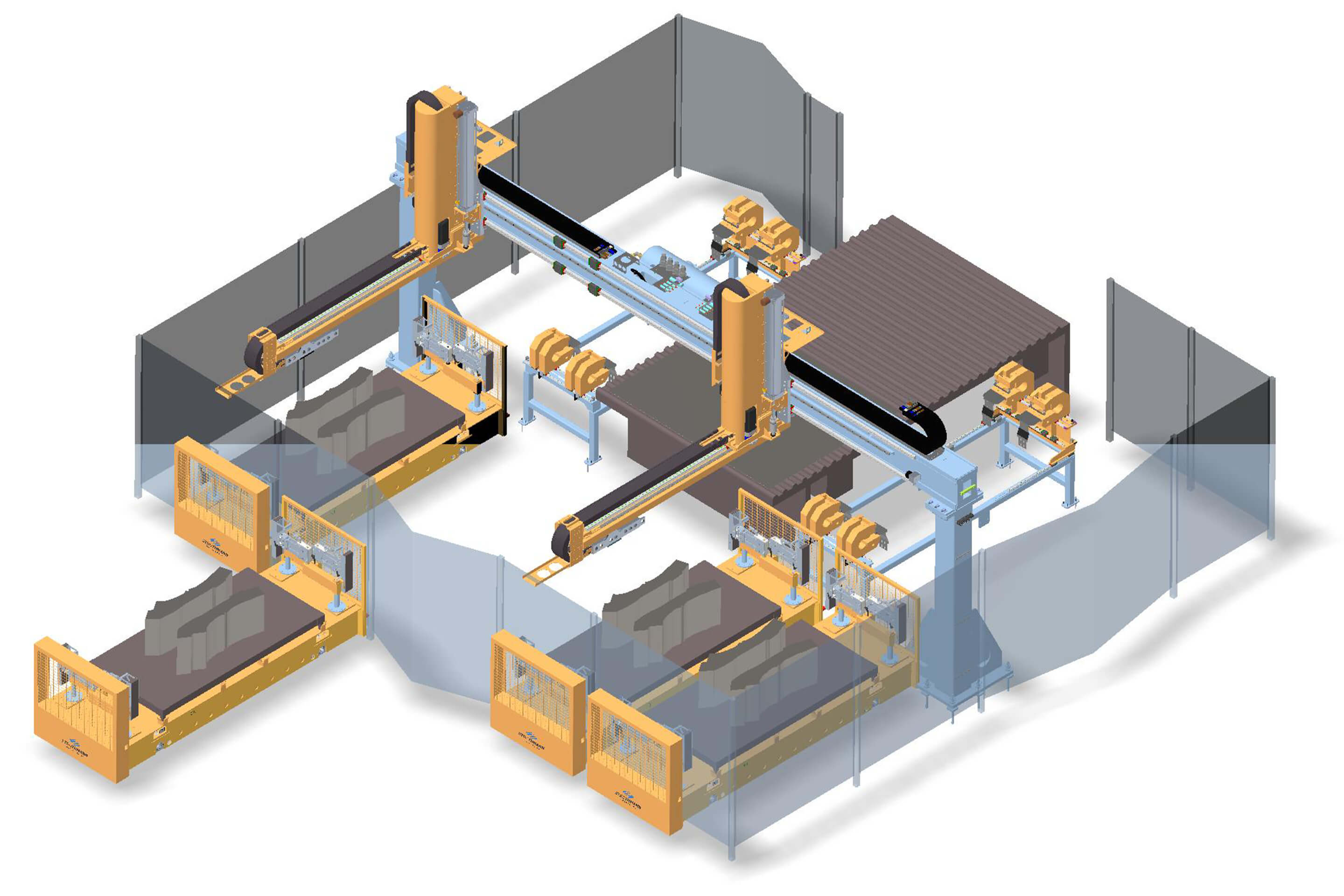
Alimentation des platines sur quatre chariots à platines entraînés sur le rail rond (changement de pile sans interruption). Les éléments de clôture sur le chariot ferment le cercle de protection
Unités d’écartement sur chariot à platines réglables manuellement
Alimentateur de désempilage 3-080 avec deux modules d’alimenteur et un axe C supplémentaire. Charge utile 60 kg
Station de marquage hydraulique ou pneumo-hydraulique incluant la mesure de double tôle. Nid de centrage intégrable
Convoyeur à rouleaux du four (mis à disposition par le client)
Caractéristiques techniques
Durée de la cadence |
Jusqu’à 10 s |
Charge utile max. |
60 kg |
Longueur de platine |
2 500 mm |
Poids de pile max. avec palette |
6 000 kg |
Axe de rotation désempileur |
± 135° |
Nombre de platines par alimenteur |
2 |
Nombre de marquages par platine |
4 |
Force de compression du marquage |
120 kN |
Temps de traitement du marquage |
env. 1,5 s |
Nombre de lettres |
jusqu’à 26 |
Chargement et déchargement de la presse
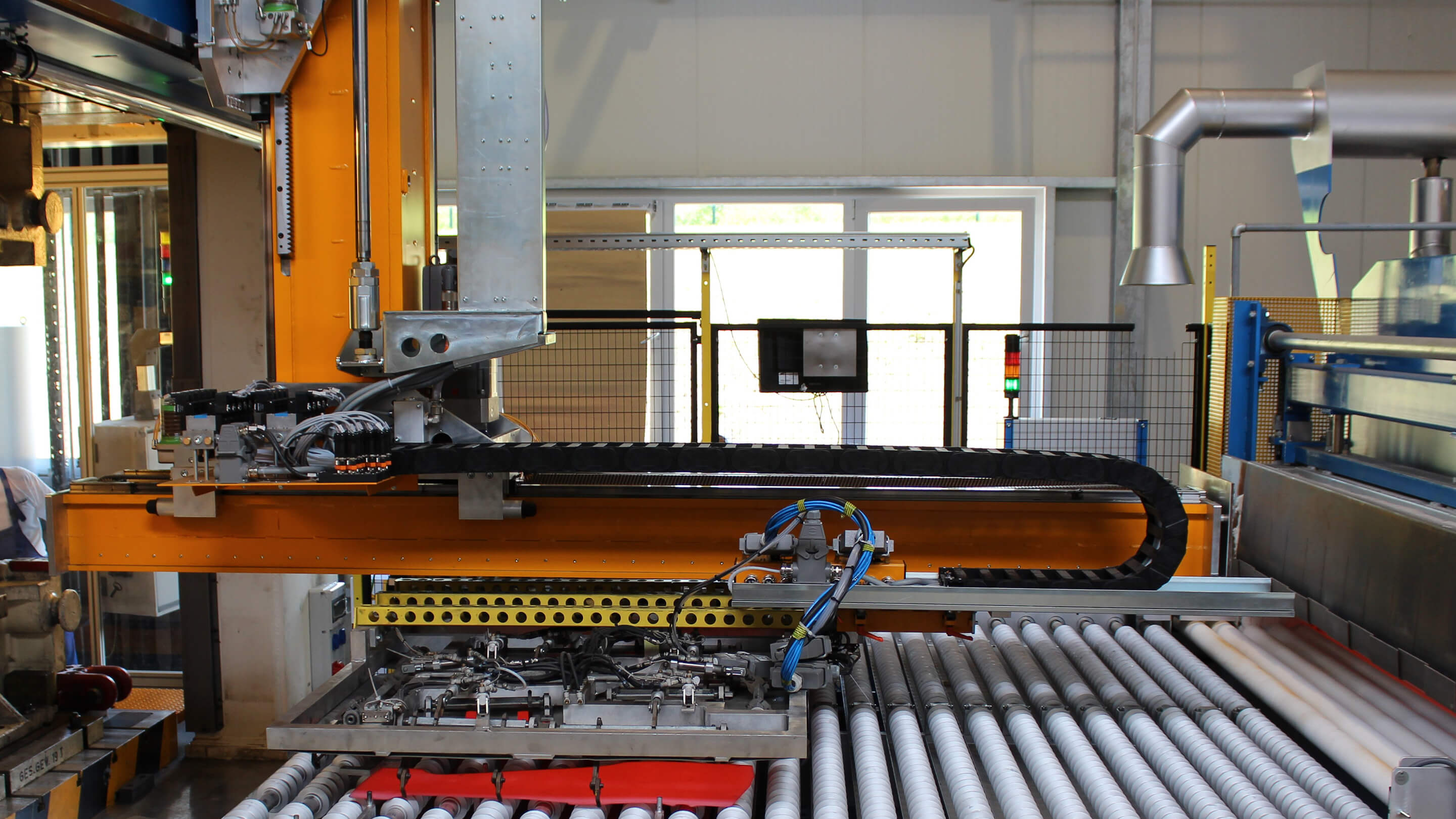
Concept d’alimenteur
- Presse dans le sens de passage dans le four
- Chargement et déchargement par un alimenteur de 200 kg ou de 120 kg
- Outillages de grande taille avec protection contre la chaleur
- Temps de changement atteignable env. 4 s
- Avantage : espace de montage compact et puissance installée réduite
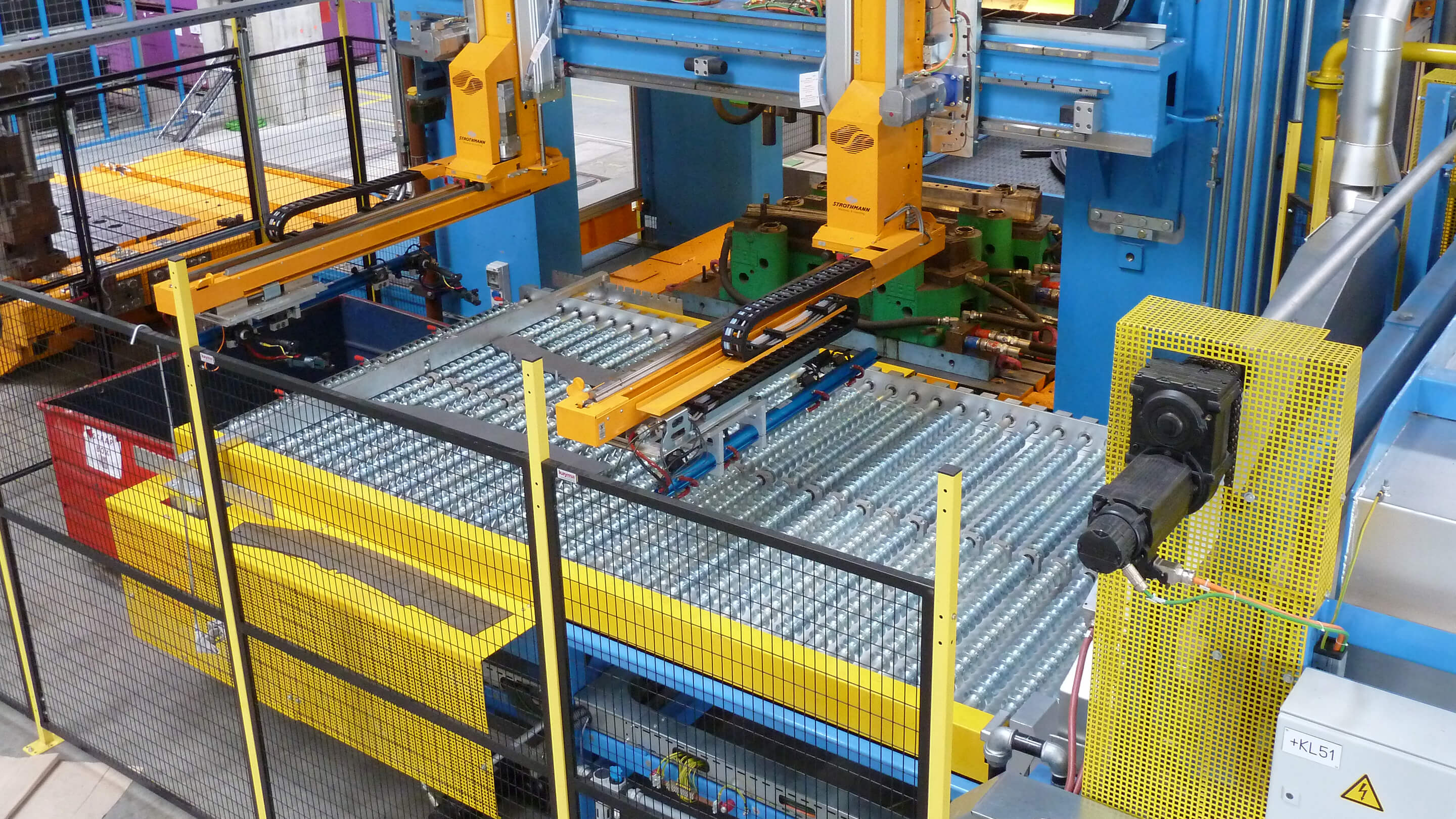
Concept de transfert
- Presse perpendiculaire au sens de passage dans le four
- Chargement et déchargement par deux alimenteurs de 80 kg chacun
- Les alimenteurs attendent dans la salle de presses à côté des outils
- Temps de changement atteignable env. 2,5 s
- Avantage : temps de cycle minimal
Concept d’alimenteur |
Concept de transfert |
|||||
---|---|---|---|---|---|---|
Taille |
1 |
2 |
S |
M |
L |
XL |
Appareil d’automatisation |
3/200 (chargeur) |
3/200 |
3/040 |
3/040 |
3/080 |
3/080 |
Course X max. |
3 500 mm |
jusqu’à 6 000 mm |
2 500 mm |
3 300 mm |
4 000 mm |
4 700 mm |
Course Z standard |
1 100 mm |
1 100 mm |
700 mm |
700 mm |
800 mm |
800 mm |
Capacité de charge |
200 kg |
120 kg |
2 x 40 kg |
2 x 40 kg |
2 x 80 kg |
2 x 80 kg |
Temps de changement |
4 s |
4 … 4,5 s |
2,5 s |
2,5 s |
2,5 … 3 s |
3 s |